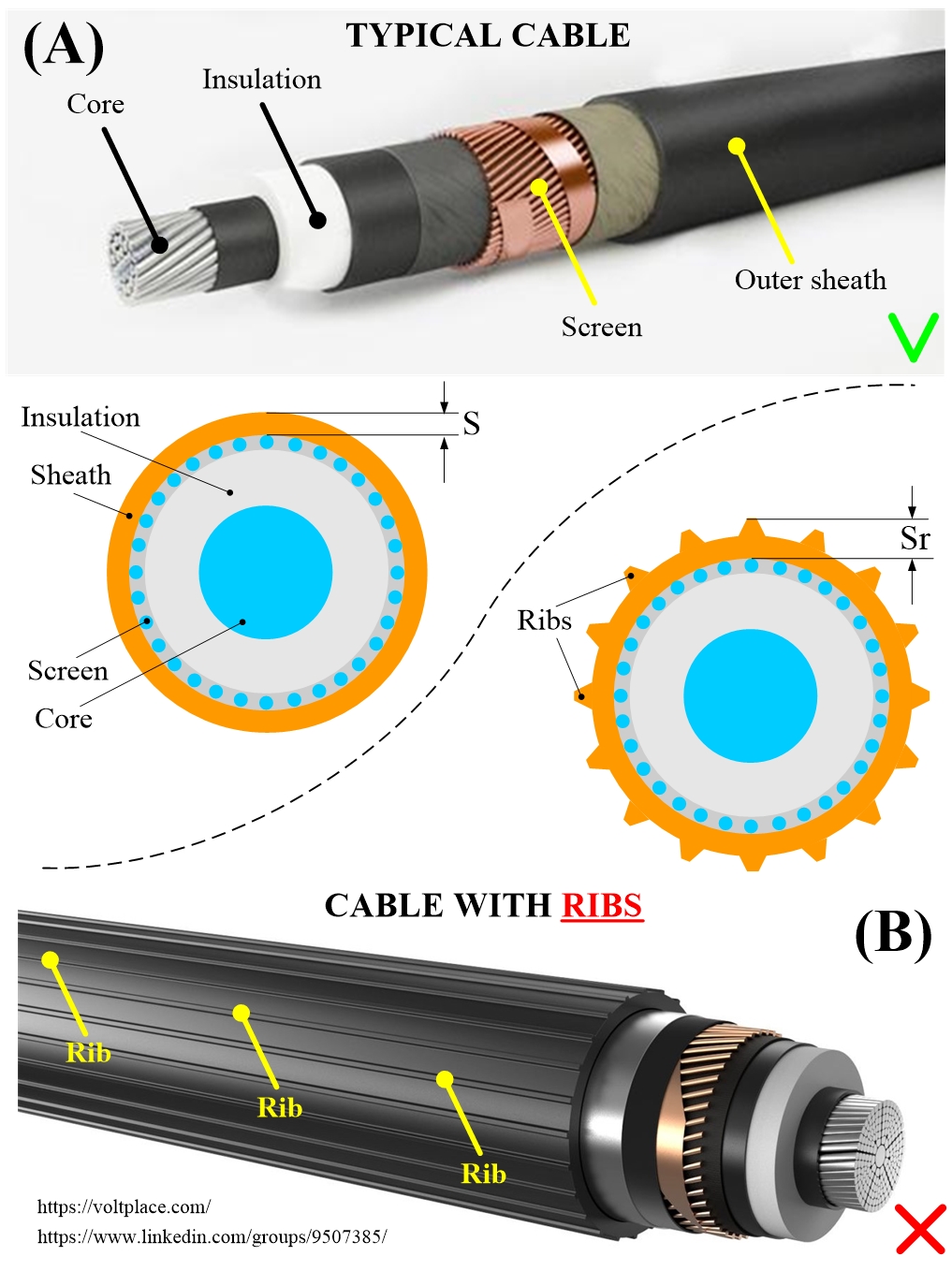
Ribs along the cable outer sheath
There are dozens of cable manufacturers in the World. They are constantly experimenting, trying to offer the market improved cable designs. Some of these innovations are not entirely successful. Unfortunately, these experiments are paid by grid companies, which get troubles during the proccess of laying cables, their operation and repair work. In my opinion, one example of an unsuccessful cable design is a cable with an outer sheath covered with longitudinal ribs.
The sheath is one of those elements that is most often prone to damage. In turn, this creates a threat of water penetration into the insulation and its short circuits. One of the ways to protect the sheath is to make it of increased thickness, that is, reinforced. A cable with a reinforced sheath is more reliable, but it is more expensive, heavier, and bends worse.
The difficult choice between conventional (A) and reinforced sheath led to the appearance of an intermediate variant – where the sheath has an increased thickness not on the entire surface, but only in some places. We are talking about a ribbed cable (B). It was advertised that a cable with ribs, unlike a cable with a conventional smooth sheath (A), would have reduced pulling forces along the route and less damage.
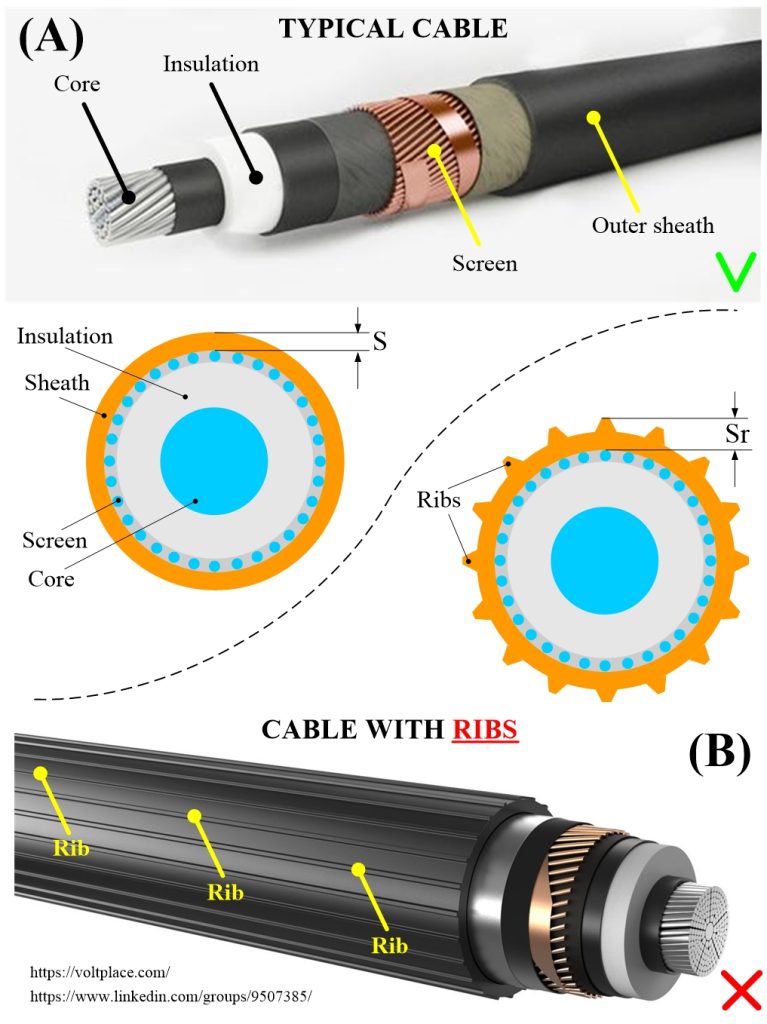
The experience gained over the past 10-15 years with ribbed cables has shown that the expected effect has not been achieved. Moreover, such cables have created problems for installation organizations:
✅the pulling forces have not changed (because the longitudinal ribs do not change the coefficient of friction and the weight of the cable, which means that the friction force will remain the same);
✅the number of damages has not decreased (because, let’s be honest, the real thickness has not changed);
✅the cap cannot seal properly the cable end during cable storage/pulling;
✅the installation of joints/terminations has become complicated (the ribs must be manually cut off and the sheath skinned, which is problematic);
✅sheath repair has become complicated (heat shrinkage does not fit on the ribs);
✅sealing of cable entries into ducts has become complicated;
✅it is more difficult for cable cleats to hold the cable on vertical sections.
If you look at it, the ribbed cable turned out to be just a marketing ploy that allowed the factories that produced such a cable to increase sales. There were three sales strategies:
1️⃣ Sell a ribbed cable at a price similar to that of a cable with a reinforced sheath (despite the absence of increased costs for materials and manufacturing, which is carried by cable factories with a really thick sheath).
2️⃣ Sell a ribbed cable at the price of a conventional cable, but attract buyers by offering them, unlike competitors, a gift in the form of a “reinforced” sheath.
3️⃣ To put ribbed cables into projects, thereby weeding out other factories that do not produce such cables.
In my opinion, the ribbed cable has brought harm to the industry, not benefit.