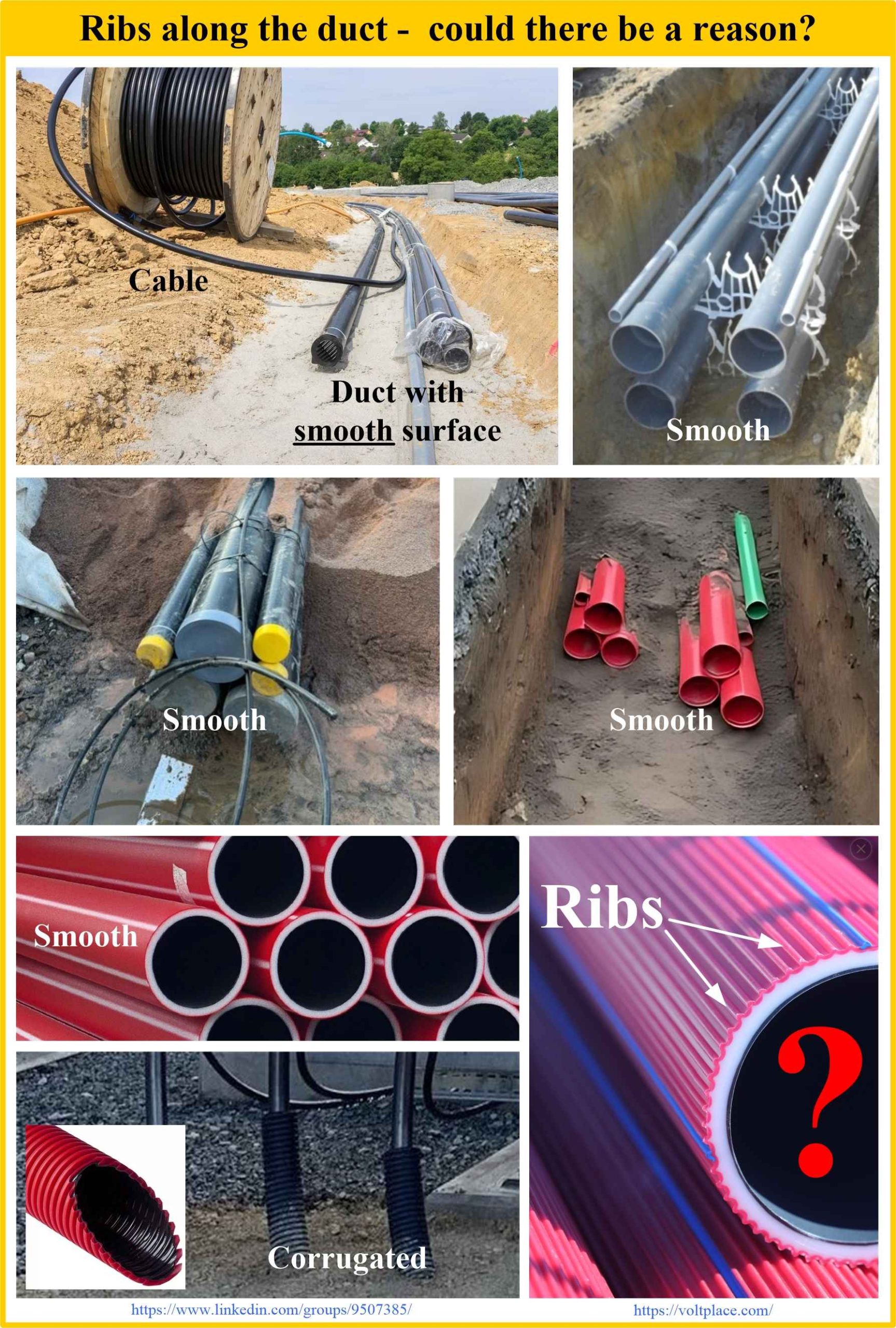
Cable duct with ribs
Cable lines (1 kV and above) are often laid in polymer pipes. In some countries, cable pipes are also referred to as ducts or conduits. These pipes/ducts/conduits allow to:
✅Protect the cable from the mechanical damage.
✅Protect the cable from the environment.
✅Reduce the requirements for the quality of trench bottom preparation.
✅Speed up cable pulling and its subsequent replacement (if needed).
✅Use the horizontal directional drilling method (HDD) for cable laying.
✅Many other reasons.
Currently, in the world, high-voltage cables are laid mainly in pipes with smooth inner and outer surfaces.
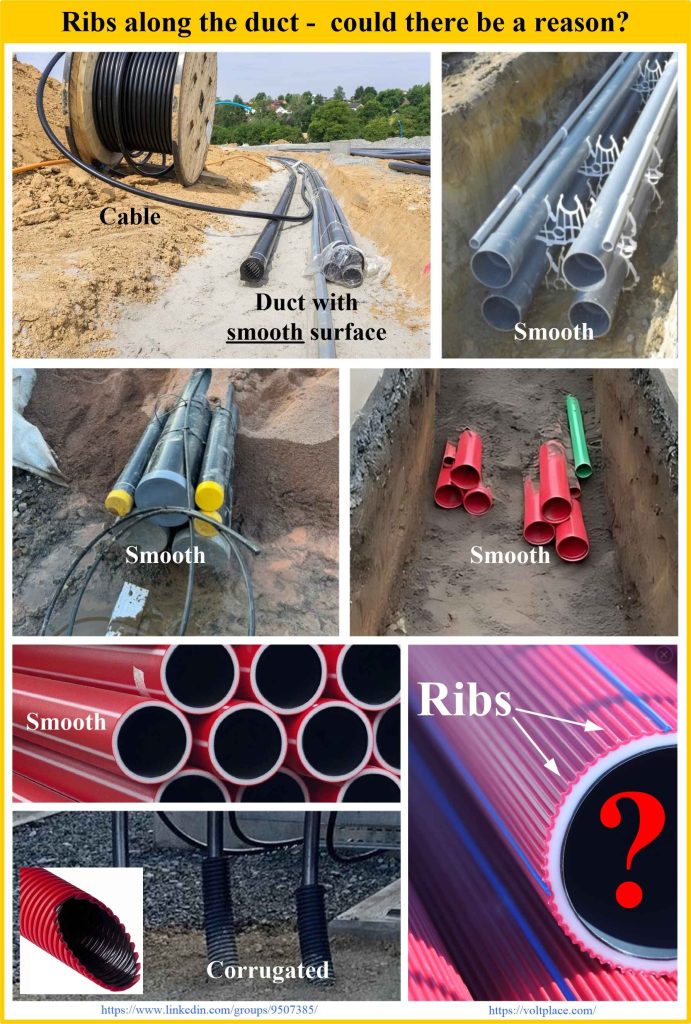
In some cases, cables can be placed not in smooth pipes, but in so-called corrugated pipes. The corrugations of the pipe act as a kind of stiffeners, allowing the pipe to withstand ground and transport pressure. Corrugated pipes are flexible, and they are used, for instance, in places where cables come out of the ground to cable terminations, as shown in the photo (bottom, left).
Smooth pipes and corrugated pipes are two well-known polymer pipe types, for each of which there is already an undisputed field of application. I was really surprised when I saw an advertisement for a new polymer pipe (PE, HDPE) for laying high-voltage cables. The new pipe has many longitudinal ribs on the outer surface, as shown in the photo (bottom, right).
I don’t understand who would need such longitudinal ribs and why. I suppose it’s just marketing. Because of the following argumets:
1️⃣When pulling the pipe over the surface the friction will not change, since the pipe material has not changed. Friction does not depend on the contact area, but is determined only by the properties of two materials that rub against each other. Whether there are ribs or not, we still pull plastic over metal or plastic over the ground, etc.
2️⃣The presence of ribs makes the pipe stiffer to bend, and this is bad. The flexibility of the pipe is important in HDD, since otherwise we will not be able to stretch the pipe along a route with a complex profile.
3️⃣The presence of ribs doesn’t influence on pipe ring stiffness (known as SN, kN/m2), since ribs are along the pipe and not across (for instance, ribs across the pipe are typical for corrugated pipe which really has an increased ring stiffnes SN).
4️⃣The presence of ribs doesn’t help the cable cooling process. In the thermal replacement scheme of the cable cooling process, the thermal resistance is dozents times (!) less than the thermal resistance of the cable outer sheath, air in the pipe, and soil. There is no point in reducing the thermal resistance of the pipe, because this will not lower the temperature of the cable, because it is not about the pipe wall.
5️⃣Ribbed pipe might have non-standard outer diameters. And this will be a problem in the design and selection of elements such as backup pipe plugs and so on.
I think that pipes with longitudinal ribs, as opposed to transverse ribs (corrugated pipe), are a bad idea.