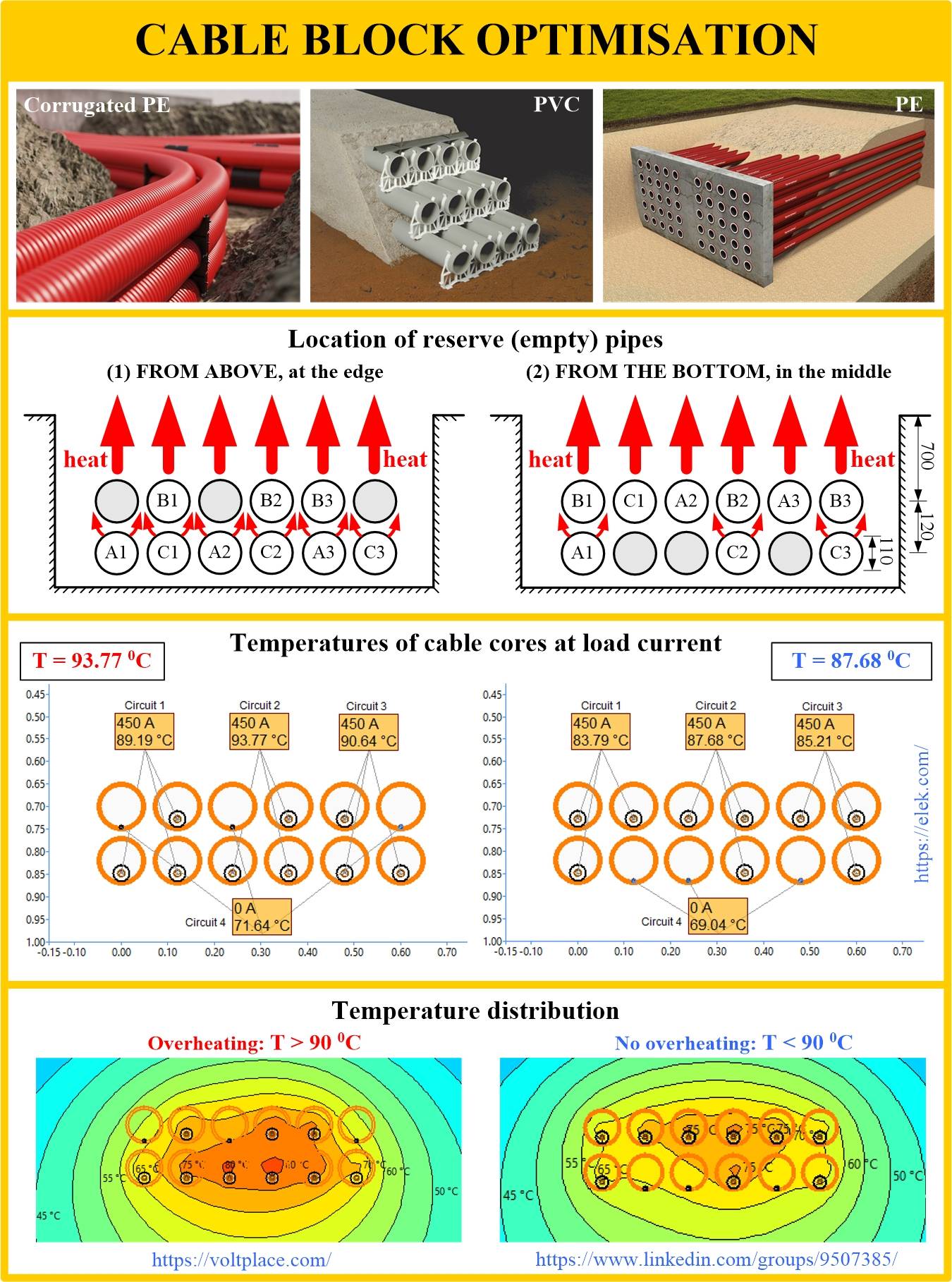
Cable block optimisation
Numerous cable lines running next to each other are usually assembled together into so-called pipe blocks. For example, this happens in areas near the switchgear, where up to several dozen parallel lines can be located in one place. Usually, the number of pipes exceeds the number of cables that need to be laid. Such a reserve is associated with several circumstances:
✅ The possibility of expanding the switchgear, i.e. connecting additional cable lines to it;
✅ The ability to quickly lay a new cable to replace the damaged one;
✅ To insure ourselves in case any of the pipes is damaged, for example, by a short circuit in a cable, and it will no longer be possible to re-lay the cable in it.
Sometimes the requirement is that up to 25-30% of all block pipes must be empty. In practice, a serious question arises – how exactly to place empty pipes in the block. For example, there are two options for the arrangement of empty pipes:
1️⃣ they are located at the top of the block, and/or on the side;
2️⃣ they are located at the bottom of the block, and/or in the centre.
At first glance, there is no particular difference in this, and empty pipes can be positioned in any way convenient for installers. However, if we perform detailed modelling in specialized software, we can see that optimizing the location of empty pipes in the block is a serious task.
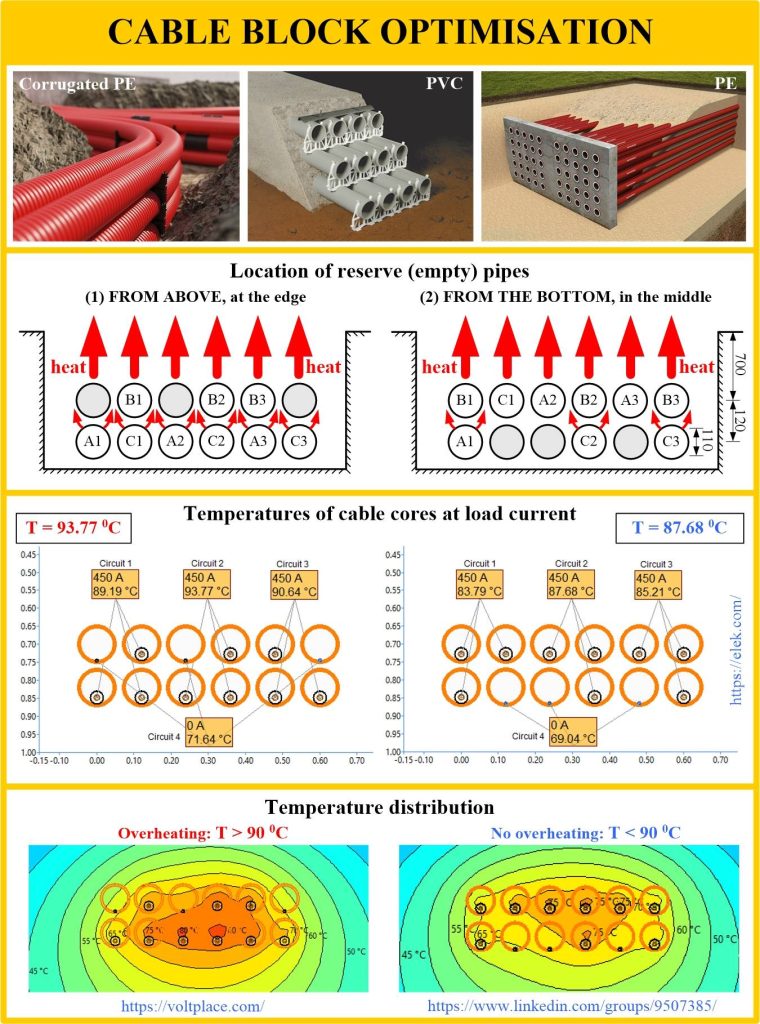
The heat that is released in the cables cores/screens rises to the surface of the earth to the air. Therefore, it is desirable that the upward path for the heat generated by hot cables be as short as possible, without obstacles. Thus, when choosing which pipes to fill with cables and which ones to leave empty, the rules should be followed:
➡️ the hottest cables should be placed in the upper part of the block and/or along its side edges;
➡️ the least hot cables (and empty pipes) should be placed at the bottom of the block and/or in its centre.
Using specialised software, it is possible to calculate almost any pipe block filled with cables of different types at different load currents. However, let’s take a simple example – there are 12 pipes (110 mm) in the photo, of which 9 are occupied by single-core cables, and 3 are empty. Note that here, to simplify the demonstration, the cable screens are single-side grounded (that is, cable lines have no losses in the screens, regardless of the distance between the ABC phases). To account for the effect of 3 empty pipes on heat flows, 3 pipes with cables were added to the model (Circuit No.4), but these 3 cables have a minimum cross-section and no current load.
It can be seen from the example that optimizing the pipes has allowed to reduce the temperature of cables by 6 degrees, which is serious, and can be used to increase:
✅ the service life of cables;
✅ the cable ampacity.
The author thanks Jayson Patrick , who provided the ELEK software, which made it possible to perform the necessary thermal calculations.
https://elek.com/